What is Generative Design?
In the past, an engineer would make a part or product by developing a drawing in CAD. The drawing would be the result of that engineer’s experience, imagination (creativity), and historical data (how similar parts have been made before). Generative design is optimization and problem solving based on a number of criteria defined by the designer. Those criteria could Structural Integrity (strength), Height, Weight, Cost Constraints, Volume of Material, etc.
But the goal here is for Artificial Intelligence (software) to generate a design or many designs that solve the problem by addressing the criteria. So, Generative Design does not necessarily mean faster although faster could be one of the criteria. Once the designs are completed, the engineer can choose the one that best suits their needs. In this way, a computer delivers manufacturable designs that solve a challenge, meet the criteria … and reach beyond the limitations of human imagination.
At the Forefront of Generative Design
Autodesk is at the forefront of Generative Design and their Fusion 360 software can simultaneously generate multiple CAD-ready solutions based on real-world manufacturing constraints and product performance requirements. A perfect real-world application for Generative Design is Autodesk’s work with General Motors to change the way car parts are made, reduce the number of parts required to make a car, and produce parts that are lighter and stronger! This will help GM to have at least 20 different electric or fuel cell cars on the market by 2023.
Does Generative Design Require 3D Printing?
There has been some misconception that Generative Design is exclusively related to 3D printing when in fact, the user is able to specify the manufacturing method including additive (3D printing), subtractive (CNC machining), casting, etc. Once the method is defined, the software will only generate designs that can be produced with that specific manufacturing method.
Generative Design is Augmented by DATRON “Next”
The DATRON neo and DATRON M8Cube are featured in Autodesk locations at Pier 9 (San Francisco), the Generative Design Lab (MxD, Chicago), and the Autodesk Technology Center (Boston). The reason for this is because DATRON technology represents the future of CNC machining and integrates so well with software like Fusion 360. The advancements the DATRON has brought to the industry impact the entire machining workflow.
DATRON “next” is a touchscreen interface with an integrated camera/probe combination (inside the milling machine) that eliminate the time-consuming task of setting up jobs. The camera shows the machining table below and the operator can select the workpiece simply by tracing the area on the touch-screen where the workpiece is displayed. Once the part is located, and the machining parameters are set, any irregularity is automatically compensated for in the software. This virtually eliminates part rejection due to improper setup. An onboard “CAM Assistant” guides the operator through the program and tool management on an interface that looks and feels like using a smartphone. All of these tools combine to help even a novice operator create a machined part in just four steps.
Keyword: Aluminum mold tooling
Excel表格技巧---给单元格插入下拉列表
You May Also Like
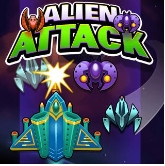
Escape Road: A Journey to Freedom
March 21, 2025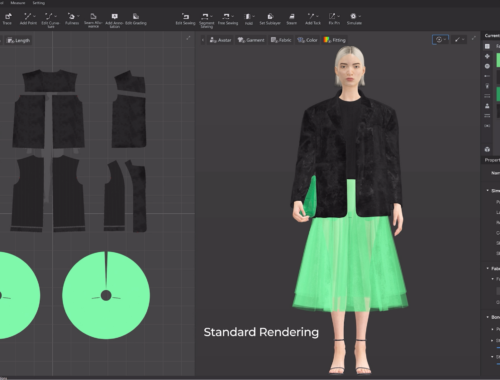
AI Meets Couture: How Artificial Intelligence is Redefining the Future of Fashion
February 28, 2025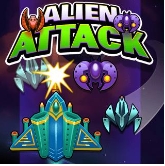