Virtual Event: A BattleBots Deep Dive With HyperShock's Wil
Ever wonder how the pros design and manufacture their BattleBots? Join Will Bales, captain of the Xometry-sponsored BattleBot HyperShock, along with Xometry's Director of Application Engineering Greg Paulsen and Big Blue Saw's Simon Arthur to find out what it’s like in the driver’s seat.
During this one-hour event, the Xometry team asked Will…
- About HyperShock's specs, from weapons to wheels.
- How did HyperShock start and when did he get interested in robots?
- How has HyperShock changed over the years and what inspired those changes?
- What materials are go-to's for BattleBots? AR500, S7, titanium, or something else?
- Why doesn’t HyperShock have wheel covers?
- How many spare parts does Team HyperShock show up with to fights?
- What trends has the team seen over time in Battlebots?
- How does someone get involved with robots and what career paths are available?
This was followed by a live Q&A from engineers, enthusiasts, and fans. Will Bales also gave some colorful commentary of his most recent match and some memorable moments from past seasons of Battlebots. Listen in as he explores everything that goes into making a killer BattleBot!
Full Transcript
Greg Paulsen: All right. Still see folks rolling in, but let's get the most out of this hour, because this is just such an exciting event today. Hey, everybody. Welcome to today's live event. This is a deep dive of HyperShock with our team captain, Will Bales. I'm Greg Paulsen from Xometry, and I'll be leading the panel discussion with HyperShock's driver, designer, and team captain, Will Bales. Also joining us today will be Big Blue Saw's Simon Arthur, who's not only a new addition to the Xometry family, but also has over 20 years of history fighting robots. So he's going to have a lot of commentary as well.
Greg Paulsen: Before we get started, let's lay down some groundwork for you all. We're going to start with some introductions, some background. From there, we're going to jump into Q and A, questions surrounding all things HyperShock and BattleBots. You the audience, you'll also have an opportunity to submit questions at any time using the Q and A tab on the GoToWebinar platform. We will try to get to as many questions as possible at the tail end of this hour, and just to note here, this is a no spoilers discussion. So we could geek out all we want up to the present. They're not going to be covering any events or outcomes that have not already been published. This webinar will also be recorded. So you'll get an email after this event with a recording that you can rewatch or share with your colleagues.
Greg Paulsen: I also have to highlight here that if you're on Instagram, we are doing and awesome giveaway. So if you follow the rules here, follow Xometry, follow HyperShock, like the post, and tag some friends, you'll be in for a raffle for a HyperShock t-shirt and some Xometry swag, I think a Xometry backpack as well. So take a look for that post and join the raffle. I think it's a really cool event there. But you know what? We're here to talk shop. We're here to talk bots, so let's just run into it. Greg Paulsen: All right. So I want to introduce the team, and the team, you all could jump on the cameras now. But let's about the main event here. So Will Bales just joined the audience. Hey, Will. How're you doing? Will Bales: How's it going, Greg?
Will Bales: Doing really well, and we've got Simon Arthur as well.
Simon Arthur: Hello.
Greg Paulsen: So I'll let you introduce a little bit, but let me give a quick synopsis. So yeah, Will Bales, team captain of HyperShock. If you don't know what HyperShock is, it's a battle bot. You can watch BattleBots fighting. They're currently in the latest season. I think what, episode four tonight? So we're relevant, right? We're right here. But Will, you're also a designer and engineer, medical devices by day, fighting robots, killer robots by night. What else do you got to say about yourself?
Will Bales: Yeah, you hit the big points. Fighting robots is the money-spending project and this money-spending job, and by day, I'm a medical device R and D engineer. I started when I was really young. I was, I think, 12 when I built my first official robot for an event, and I was hooked ever since. So I learned how to tinker on things. I learned how to use machine tools, how to use CAD and how to get parts made. I had my first foray into contract manufacturing when I was 15, when we had some parts that were too complicated. So we sent them off to China and learned about that whole process and staying up until four in the morning, trying to talk to people. So yeah, BattleBots and robot building has formed my career as an engineer.
Greg Paulsen: That's awesome, and again, we have a bunch of questions to ask you about that, for sure. I also want to introduce … So Simon, you are both a cohost and panelist. You're here because you're awesome. Simon Arthur, he's the founder of Big Blue Saw. Big Blue Saw is now a Xometry company, and he is the maker of all things flat, so water jet, laser cutting, you name it. You started early, right? Robot battles, 1997-ish or so, so 20-plus years?
Will Bales: Right, right. Yeah. I started at robot battles here in Atlanta, Georgia. There's a competition called Robot Battles that was running for several years, even before I started, and is actually still going on now, happening Labor Day weekend again this year. I saw that back in 1996, happened to be attending the Dragoncon event, and Robot Battles was there. Marc Thorpe, who was the creator of Robot Wars was there, and he was showing off not these smaller robots, which we had at Robot Battles. He was showing off these big monster things from the old days, the robots like the Master and Blendo. That really got me hooked on robot fighting, and eventually that led to me wanting to go into my own business where I could make robot parts. That was Big Blue Saw, and then we merged with Xometry back in November this year or last year.
Greg Paulsen: That's really exciting. Yeah, I've also realized there's a lore of BattleBots, because depending on who you're asking, it's either season 11 or season 6. There's the before and after times. But yeah, Simon, you had some BattleBots, Neptune and Death Ray. So it was new season two, as you described to me, or old season four, five, six. So just again, I'm super, super excited.
Greg Paulsen: Before we get into the Q and A, I want to just tell you like, "Wait, who the heck is Xometry, and why do they have Will Bales here, speaking about this?" So Xometry is an on-demand manufacturing company. We're a digital manufacturing marketplace. We connect buyers, so people like Will, who need parts made in all sorts of manufacturing technologies, with the suppliers. So you go to a single place. You're able to get instant quoting, get parts, like, for example, this battery box here or CNC machine cam pieces. Will's got the battery box in Will's hand right there. It's a one-stop shop for manufacturing. Actually, as a sponsor, we make parts for them. We also are able to have cool little things, like Xometry logos on a super hip bot.
Greg Paulsen: So I wanted to show this really quickly, just to kind of show you how this works in practicality. So you have someone who is designing a 3D model using popular 3D CAD programs. You could upload that. So this is Xometry's website, and it'll default to a process where it's guessing what you're going to do. In this case, this is that battery box we're talking about and just very quickly you can go and configure it. You could specify exactly what you're looking for. In this case, with Xometry, we have for 3D printing six type of polymer-based additive manufacturing processes under each one of those materials available, like fused deposition modeling. We have two metal 3D printing processes as well. I'm just saying next season, Will, take a look at flame retardant ULTEM 9085. Could be really
Will Bales: I know. I know.
Greg Paulsen: … good if you have any battery fires. But the one that you were holding was made out of polycarbonate. So a 3D printed polycarbonate battery housing. I have to give a shout-out. When Xometry merged with Big Blue Saw we all of a sudden had this capability of sheet cutting. So just as easily as you could get a 3D print, we could do things like machine or water jet cutting. In this case, I just saw you took a little gear piece here, and you can see that if you could source it, you could cut it with processes like water jet.
Greg Paulsen: That includes these bot favorite materials, like AR 500. So just wanted to highlight that in my minute and 40-second demo of Xometry's site to show how easy it is to actually get stuff now, versus what you may have experienced in the past with working internationally, calling, working between 12-hour time zones and all that. We have domestic. We have international. We could really make that work, make that effective. Let me go through. But again, we're here to talk question. So I'm going to at the questions, the Q and A session. Let's walk through the specs, Will. What is HyperShock? If someone's like just out of blue, they see that and they see it, how do you describe it? What's it made out of? How's it work? What do you do with it?
Will Bales: The elevator pitch, right? All right. So HyperShock is a 250-pound fighting robot. It has brushless motors and big lithium batteries and a big, scary weapon and go-kart tires. It rips around a 48 by 48 arena and tears parts off the opponents and hopefully throws them up in the air in the process. We use everything. We've got titanium armor, the AR 500 armor. We have aluminum armor. There's carbon fiber pieces. The frame is all AR 500. The weapon discs are S7 tool steel hardened. We've got 3D printed components inside. We've got formed bits, welded bits, machine bits, lathed bits, C and C and manual. We've got everything. Everything's in here.
Greg Paulsen: Everything's in this, and it's configurable, too, right? So depending on the situation, you may actually change a little bit of the layout based on the bot you're fighting.
Will Bales: Yeah. For example, in that picture, there's the wedge. But if we're going up against another vertical spinner with long big fork-y things in the front, we might want our own forks. So we can swap those things out. If we're going up against a big horizontal spinner, we have a different weapon configuration that's a single thicker disc in the middle. It's like two inches thick so we can take a beating better. So you can swap out the weapons. Some robots have completely different weapons systems, and they'll go to a hammer instead of a spinning weapon or a flipper. So there's lots of variety, but ours is pretty focused on the four wheel drive scary spinning thing.
Greg Paulsen: The four wheel drive scary spinny thing. Yeah, also noting I was looking at your site, just doing some research here, and the tires and everything, you're using kind of go-kart pieces for that. So there's custom mixed with COTS, right? Commercial off the shelf items.
Will Bales: Right. Yeah, exactly. For example, this is one corner. It's the axle. It's a hub. Those are two different machine components, and then we have the tire, which is a go-kart tire. We have a go-kart rim that we powdercoat, make it nice and pretty. Then because it's a pneumatic tire, we foam fill it so it doesn't go flat. So when Tombstone comes along and rips a chunk out of it, it can keep flailing around and give us enough traction to move around the arena. Yeah, you're absolutely right. It's a combo of off the shelf stuff and custom components.
Greg Paulsen: I just have to ask. Triple expanding foam, is that what you're using, like the Good Stuff foam, or is it something a little bit more
Will Bales: We're a little bit fancier. It's Smooth-On FlexFoam-iT! IV. So nice and spongy, relatively lightweight. The 35-second working time is a little challenging, but we have a method. There's a kitchen mixer involved. It works.
Greg Paulsen: Nice, nice. If you want to, I'd love to hear your commentary. Just we want to see it in action. So this was last Thursday. Would you be willing to kind of walk through? Also, I can't project sound, so definitely need someone to talk through this as well. Will Bales: Absolutely. I'll do my best to put some sound effects on.
Simon Arthur: Robot fighting time.
Greg Paulsen: It is robot fighting time. I am not quite the announcer, but we'll go with it.
Will Bales: Faruq does a much better job than I do as well.
Greg Paulsen: Oh my gosh. Oh my gosh. So the HyperShock versus Slammo.
Will Bales: Right. So this is the first time we got to drive this thing.
Greg Paulsen: Boom. Will Bales: So when it starts hitting stuff, we're excited, but we're nervous, because Slammo is really thick. It's like a half inch thick, super hard, high manganese steel. I forget what it is.
Greg Paulsen: Very tough.
Will Bales: But we were worried that the weapon was just going to blow up. This year, we went to thicker discs, because last year, some of our team or fellow teams, Witch Doctor, had a failure of S7, where the discs were failing on them uncontrollably. So we were a little worried.
Greg Paulsen: That was a good hit.
Will Bales: So we bumped up the thickness. Yeah, there were some good hits in this one. We bumped up the thickness, and to make the weight work, we had a magnesium central hub there. So that big yellow bit between the two weapon discs is a nine pound, seven pound big magnesium five access machine bit. We were worried that that wasn't going to hold up to snuff, and you never know until you've finally hit something. So at the end of this, the relief is it did the thing, and it's not in multiple pieces.
Simon Arthur: So what do you think you were doing with the S7 that the other teams weren't doing? I mean, why were they having problems, but you weren't?
Will Bales: Witch Doctor in particular, it looks like they had a bad batch of material or something. They did a massive deep dive into it, and they sent it out to some metallurgist research facility. They did this whole analysis and old disc versus new discs. So it was definitely something to do with just luck of the draw, bad material. But they were the thinner dimension. People are hitting harder. The floor is thicker now. So they're transferring more energy back into other robots, because if you're a vertical spinner, you're spinning up. You're hitting half your energy up and half of it down. Well, if your discs can't handle that extra load from the floor flexing less, then they might start to break. Will Bales: Our design, our tooth design is much sharper. Our goal has always been to tear through things and cut nice chunks out of people instead of the blunt force hit you with a baseball bat kind of hits. So we think that that definitely helps us in our design choices and our fortune so far with no broken discs. But just to be safe, because we were beefing up the front end of the robot this year, we did thicken them up so they're an inch and a quarter now instead of an inch. But they're hard, 57 Rockwell C.
Greg Paulsen: Gosh. I was going to say it's interesting, because you're talking about … We're jumping ahead, but I love this. You're talking about using a magnesium hub, which is actually a very lightweight, but strong metal. Also, we know magnesium here requires its own fire extinguisher by your machine when you're running it, because if you ever see someone that's like, "I melted my lathe," it's probably magnesium is the reason why. But you have titanium. You have all these other components, and then you have where the action is. It's something that just bites and destroys there. But let's take a walk down memory lane really quickly. You mentioned you started when you were young. But what was the origin story of HyperShock? Where did you start, and then when did HyperShock start?
Will Bales: Right. So the origin story is my dad was a First Robotics coach. So I went to First Robotics competitions as a kid. when I started to get old enough, it was right around the time that BattleBots had this program called BattleBots IQ. You had to be 12 in order to make a 15-pound robot.
Greg Paulsen: Wow.
Will Bales: So as soon as I was 12, my HyperShock teammate, Tyler, and I at the time and another kid, Benji, we built a 15-pound robot. It was an upside-down 14 inch wok from Kmart that my mom bought, and it had some bolts coming out the sides to act as whackers. We put black and white duct tape all over it so it looked like a cow "hefer-butt." We won our first match against somebody who had a turtle shell for armor, and we lost the second one because our batteries in the transmitter died. Ever since then, we were hooked. Will Bales: So then fast-forward to 2015. Tyler was just, was graduating college, and I was working in Boston. We got a phone call from Trey, Trey Roski, one of the executive producers of BattleBots, saying, "Hey, we're going to bring this show back. You want in?" We said, "Absolutely. Please sign us up, whatever it is." So we ended up getting all together from different parts of the country where we all were, and we formed HyperShock. We've been doing it ever since.
Greg Paulsen: That's awesome, and just tell me about the team now. How big is that team?
Will Bales: So when we started, it was four dudes. We were four young 20-somethings working on the robot. Now it's grown. We've had people come and go. Now, at one point at the event, we were 11 people, between absorbing some of my family who was on a different team, Mohawk. The rest of my family was on the different team. It's a long story.
Greg Paulsen: What a feud. Will Bales: Yeah, yeah. Good family feud. So we absorbed them, and we got some new teammates. We've built up this massive crew now, and so when we show up to the event, we've got two different teams working on each separate robot. For the first time this year, I was able to just kind of sit back and relax and not have to do anything. It was so delightful. I could walk around and talk to people and see other people's stuff. It was the best.
Greg Paulsen: That's awesome. I mean, it's just amazing to see how it's grown and just honestly how the industry has grown. I have to ask before we jump into kind of changes. On design-wise, were you CAD-driven? I mean, obviously if you're using a wok, you're using some something else, but when did you start becoming more CAD-driven in your design?
Will Bales: So when I was 14, my now boss over the summer taught me how to use SolidWorks. I squandered all that mental energy on designing robots, designing more robots. So that was part of the reason I ended up learning all about machine shops in China and staying up until four in the morning on school nights, talking to companies to try to build these parts that I'd dreamed up in CAD. Learned all about designing for manufacturing. Yes, you can make the most of everything, but sometimes you shouldn't. So we've kind of grown with that, and now there's a lot of sheet metal and learning about how to efficiently design things so that you can manufacture them quickly and efficiently and cost-effectively.
Will Bales: So now everything is CAD. We are designing in CAD up until the very last minute. I think our last part that actually made it on the robot we designed, I designed, I think Tuesday morning or technically Wednesday morning. It was like four in the morning. There's a lot of four in the morning in robot fighting. It was like four in the morning the Wednesday before the event started. That was the last part we designed, and we're doing everything right until the last minute.
Greg Paulsen: Well, I mean, I hear sometimes your notice for when the competition is isn't that long, either. So it's always you're kind of prepared, but it's always up to the wire, too.
Will Bales: Absolutely. There's all that time between midnight and 6:00 AM that people waste sleeping.
Greg Paulsen: Sleeping.
Will Bales: We leverage a lot of it.
Greg Paulsen: That's awesome. So just talking about design, talking about evolution, what has changed over the years? What have you seen as major pivots or milestones in your robot fighting career, especially with HyperShock?
Will Bales: Okay. So the overall ethos of HyperShock has stayed true through all six seasons that we've competed. So four wheel drive, big, scary spinning thing. We started with the vision of also having some flippy arms on the front, and we've tried that a couple different ways. Unfortunately, it's just added complexity and unnecessary weak points and cost. So especially this year, we've fine-tuned the scope, if you will, to just a really fast drive train and a robust weapon system, instead of trying to do that and something else, because there's always the compromise. When you have a 250-pound weight limit, gravity doesn't sleep. You can't just sneak a couple extra pounds in for a self rider just because you feel like it. It has to come out of somewhere.
Greg Paulsen: Yeah. I think you have the little ears, too, right? So your weapon doesn't stop.
Will Bales: Yeah.
Greg Paulsen: You have the ears that aren't just for flair. They're functional.
Will Bales: Exactly.
Greg Paulsen: So you don't blast off by hitting the weapon on the ground.
Will Bales: Yeah, yeah. Season one and season two, we attempted single piece carbon fiber monocoque frames. Season two worked out all right. That was the year that we hit a drone with a rake, and it held up. But especially when we started, season one and season two were you had a fight that was kind of your placing round, and then from there, it was a single elimination tree all the way to the finals. But they changed the format to these fight nights, which gives a lot more fights per robot, which is great, and a lot more practice. But it means that you might have to go through three or four really scary fights before the tournament, and that means you'd probably have to have multiple chassis. We didn't want to make half a dozen carbon fiber frames, and our hands hurt from all the carbon fiber dust. We said, "No more of this." So went back to sheet metal for everything.
Will Bales: Throughout our whole design, aesthetics was definitely important to us. Our goal from day one was make it cool, make it exciting, get a toy. So every year since then, it's like, "Okay, would this look good on a Target shelf? If I was a little kid, would I want this?" That's been a goal of ours ever since, because this is a passion project first and foremost. So it needs to be fulfilling for us and fun for us and a good design challenge for us. So we keep it that way.
Greg Paulsen: That's really awesome, and you mentioned this. I think for a lot of people the point on the radar where HyperShock may have showed up. So I have to show the clip. I have to show the clip here. Will Bales: It's a good clip.
Greg Paulsen: Yeah. So this is … Let see if I press the … All right. It'll play. HyperShock warrior clan. Will Bales: Yes. So for those of you who haven't seen this episode, early on
Greg Paulsen: I'm going to pause here just for a second. Will Bales: Yeah, yeah, yeah. So some context. In season two, they told builders, "Hey, you could have a drone, and you could put a flame thrower on it." There were limits on size, and it was like 10 pounds. You couldn't have more than a certain amount of propane. People started to do it, and our team said, "Well, that's stupid. What's that going to do? Wouldn't it be fun to somehow make them look bad and just swat them out of the sky somehow?" So long story short, right before the event started, my mom was at the Home Depot, and she called us and said, "Hey, do you need anything?" My teammate Tyler, who operated the arms that year, said, "Grab a rake." So then we went into this fight thinking, "Okay, this robot that has this massive fire-breathing drone, let's just swat it out of the sky."
Greg Paulsen: Yeah. So let's play the clip. All right. So this is the flame-breathing drone here.
Will Bales: Yep. So it's a two-part robot. So there's the thing on the ground, which has this big spinning thing, and it flips and then the drone that's now also on the ground.
Simon Arthur: Oh.
Will Bales: It breathes fire. We were terrified that we'd look like total idiots flailing this rake around and we'd be beaten up, but turns out that
Greg Paulsen: 10-foot hit. Yeah.
Will Bales: Yeah, yeah. It turns out a $12 rake can take out a $1,000 drone just fine. After that, you didn't see many drones. Greg Paulsen: On that note, because I'm watching some of the Q and A again, we're saving a lot of the Q and A from the audience until the end. So keep on asking. It's going to be long. But there was one that's from Amanda, said, "My five-year-old son would like to ask Will Bates, during the battle … Oh, with Battle Royale with Cheese, why did they go after the mini bot first?" So there's a lot of mini bot equity as well going on.
Will Bales: Yeah. Well, mini bots are cute. Yeah, in that particular fight, season three, it was after we had gotten our butts kicked by Bite Force, who ended up winning that season. So I think the producers felt bad and said, "All right. You need to do something." So they gave us a fight against Battle Royale with Cheese, and they were having issues, too. So we thought we'd let them spin up, because in the test box, they were able to spin the bacon spinner. Yes, it was a slice of bacon on a burger robot. It was great. So they had the bacon spinner that could spin up just great in the test box.
Will Bales: So we said, "All right. You take your time. Spin up. At least it'll be a good match," because the worst thing that happens to anybody, the show or any of the teams involved, is your fight isn't worth airtime. You get highlighted in the past or sometimes it just makes it to YouTube. Some of the YouTube fights this year were actually really great. But in the past, it's been a demotion. So we said, "All right. Just spin up, and we'll figure out something to do." That little mini bot's just sitting there, minding its own business, and I've got to do something. So guess what? The mini bot gets punted.
Greg Paulsen: That's the end. RIP, mini bot there. No, it's so interesting just seeing the mini bots and seeing when they're there, when they're not there. So yeah, let's go into it. Let's go back in the details. But I really love the ingenuity. I also love that there is some showmanship, right? There's practicality. "I have to destroy my opponent's robot." But there's a flair. Definitely HyperShock is known for that flair.
Will Bales: Yeah. Like I said, we want to be fun, right? So it needs to be entertaining to watch. If it's entertaining, win or lose, then we've done our job.
Greg Paulsen: Awesome. All right. So let's talk heavy metal. I kind of want to sit back, too, especially with you and Simon onboard here, because you live in the metal here. I know how it's cut sometimes. But yeah, beyond this ranks. What are the popular materials? What's your BattleBot made of? What are you against? Just go through some more of that logic.
Will Bales: All right. So the elephant in the room is obviously AR 500. You hear it almost every episode on the show. You mentioned it in the demo video at the beginning of the webinar AR 500 is most common … For everyday use, you'll see it on a bulldozer or some kind of excavator. Big, heavy machinery that's abrasion-resistant is a requirement. So the AR is abrasion-resistant, and the 500 is the Brinell hardness. There's AR 400. There's AR 500. There's some companies that make AR 600 or Armox 600. You might hear it. It's all about how hard it is, and you're trading off a toughness and how durable it is and how hard it is on the surface and how hard it is to cut. So a lot of teams use AR 500 both for weapons and for armor, because it's pretty darn tough and it'll dish out some pain. It's a very common material. I'm sure, Simon, you guys cut it all the time.
Simon Arthur: Oh, yeah. Oh, yeah. Definitely, especially around robot building season.
Will Bales: So that's definitely the most popular.
Greg Paulsen: Yeah, and I was going to say, I think just Simon, kind of talking your origin story, the origin of Big Blue Saw was it was just hard to source this stuff, right? It was just frustrating and trying to find someone to cut this, your metal.
Simon Arthur: Right. Yeah. At the time. So I started Big Blue Saw late 2005. Kind of the genesis of the idea came out of a little get together around Dragon Con time. It was just so hard for everyone to find the machine shop to make the parts, and then sourcing the material on top of that was a huge, huge hassle. So I thought, "Well, I know a couple shops who I might be able to work with." My day job and my day job for many years was software engineering and developing websites and so forth. So I thought, "Why don't I just put this out there? I'll make a website where people can order custom parts, and I'm sure if our little corner of the world doing fighting robots is having this kind of problem, there's got to be other people out there who are having similar issues." So that's why I created Big Blue Saw and launched that back in '05.
Greg Paulsen: A company designed around … It cuts other stuff, too, but designed with inspiration, just the frustration of sourcing, which is also something that Xometry obviously empathizes with, is our whole goal is to make sourcing stuff super easy without all this back and forth. So it's just a really great match there.
Simon Arthur: We try. We try. It's still kind of tricky to get the right piece of AR 500, but we've worked with our suppliers, and now we have that. We even keep some in stock back in shop, too. So we have that, and it makes it a lot easier for the robot builders, especially if they're under the gun, to get their materials cut through us.
Greg Paulsen: Yeah, no, I do want to ask, just Will, on CNC machining, a bread and butter material for normal is something like aluminum 6061, or you could go 7000 series, which is usually kind of lighter, stiffer, used in aircraft. Where does that play a role? Does that play a role anywhere on HyperShock? Because I've seen it around, but it's not your weapon, right? Yeah.
Will Bales: Yes. That's a great point. I agree. 6061 is the bread and butter of what most people are using, and it works pretty well. One of the big problems with 7075 is it's so brittle. Yeah, it's strong, but especially in robot combat, people try to predict where the hits are going to come from, and you're always wrong. Everyone tries to do FPA or some fancy thing and try to model the kinds of hits that we get, and it's never quite right. So what a lot of people have found is they'd much rather an aluminum part bend or somehow yield rather, than just fracturing, because I'd rather have a bent frame than a cracked in half frame. But we've used 7075 in the past. This year, we had a little bit of 2024 in some critical areas, where it was a little bit more tucked in, not quite as brutal as 7075. We also like
Greg Paulsen: 2024's closer to the forging. So it's machinable, but a lot of times, it's compared to forged aluminum. Yeah.
Will Bales: Right. We do like 6061 a lot, because you can anodize it fun colors, though.
Greg Paulsen: Oh, by the way, I got some heat from a question. So I asked this. Sam asked, "That anodized gold part on its own looks cool, but it doesn't really fit the overall color scheme, Will." So I answered this, "Come on, man." Simon Arthur: You can't go wrong with gold. Will Bales: I mean, it looks pretty cool.
Simon Arthur: Gold's beautiful. Yeah. Will Bales: We tried to come up with some other colors this year. The fluorescent pink is really hard to do, and especially for some of these bigger parts that we didn't have the facilities for in our workshop, we sent them out. It was a lot easier to do gold as a cool color, and it was one of those colors that's available. It turns out it's really difficult to find a shop that can do one or two-day turn funny color anodizing.
Greg Paulsen: Yeah. They need to set their pigment batch just for those specific parts, which is
Will Bales: Exactly.
Greg Paulsen: … the big thing there. That's also my plug for Xometry's finishing services. But anyways
Will Bales: Yeah, there you go.
Greg Paulsen: … I didn't want to say, because you were talking, and actually, you were talking about another robot. You were talking 6061 versus other ones. By the way, I'd have still wrapped here my nice 6061 water jet Xometry X, which working on some signage, but to your point, 6061, compared to 7075, it's more malleable. But I don't want bend it. So you were talking about a bot that had something with a high manganese content, and manganese makes stuff ductile, which means when I bend it, it stretches first. It doesn't put cracks, especially along the grain. So usually if someone's choosing a sheet formed part, it's probably a 5052 R manganese content introduction.
Will Bales: Exactly. So all our side armor, which is all bent in funny shapes, that's all 5052. Good call.
Greg Paulsen: All right. So yeah, any other questions about metal and stuff? This is actually the right audience. So please, folks, I see a lot of questions coming in, so I'm really excited for the Q and A. But yeah, keep it going. Also, someone asked this question. There's probably two questions already from the audience about this. I had to plug it in as well, but short and quick. Come on. Why doesn't HyperShock have wheel covers? I think you answered a little bit beforehand, too, with kind of your points there, but just want to hear it again.
Will Bales: Right. Okay. Two to three answers. Number one, it looks cool. We wanted this race car toy aesthetic, and race cars don't have big old protective things around the sides of their wheels. So we wanted to show off the tires. They look cool. Two, when you have wheels on your robot and you want to protect them, usually you go smaller, because the bigger the tire is, the more material it takes to protect it, and the biggest fear we have is that you put some let's call it light armor on the outside, eight-inch titanium, grade five titanium on the outside. That's what we did season one. We actually had a sandwich which was eight-inch titanium, a rubber sheet, and then a 6061 aluminum sheet to try to take some shock loads.
Will Bales: We had a fight. It was not much of a fight, because we weren't really working, but we had an exhibition fight against Ice Wave, and he went right through it and peeled a claw into the tire and jammed the wheel. So pretty quickly, we realized that you can either armor the wheels poorly and it gets bent in or somehow impairs your ability to drive or you can put thick enough material there that you don't have the weight to go elsewhere. So we just said, "Well, we'll take our chances. Drive's pretty good. For the most part, we can kind of pick our shots and where we take it, and we're very maneuverable. So that definitely helps."
Will Bales: We found this tire solution, which is pretty lightweight. Frankly, we used it as a giant stiff arm to keep other robots away from the really important bits. A tire like this and a wheel and the foam in it and the tire stickers is like $131 for us, which sounds expensive until you consider other robots which have machined billet 6061 hubs, and then they're urethane casting those and they're $400 or $500 apiece. I'll happily go through four of these a match and keep throwing new ones on as long as the expensive bits on the inside of the robot stay safe. So we've used them as an expendable, sacrificial keep away stick around the outside of the robot, and it's working really well. So yeah.
Greg Paulsen: I think you mentioned, too, the maneuverability that you have and that you're demonstrated. It's not maneuvering itself. You're saying that you're driving the thing. So, I mean, kudos to the driver as well, right, and to you, Will, by the way. Will is the driver, for the audience members who may not make that connection. But yeah, I think that's something to show, is you really are zipping around. It's 250 pounds of fighting power that's just flying around, and I have like 1,000 questions about gyroscopic forces, about your spitting wheel and how you've learned to compensate with that. But for the sake of time, I'm just going to go with let's talk about the pit. Let's move to these bots get damaged. What does your normal show-up BattleBots … This season's Las Vegas. What comes with you for those fighting events, and what do you have access to?
Will Bales: So when we started, you showed up with one robot and maybe some spare electronics, maybe some spare motors, and that was it. You showed up, and there was Lincoln Electric there to help you pound stuff back and weld it back into shape. That was enough, and then robots like Tombstone and Witch Doctor and Ice Wave and Minotaur started destroying people's robots in a way that was unsalvageable. So everyone started to show up with more and more spares, and so now cut to the present. It's standard fare for people to show up with two built robots sitting next to each other.
Greg Paulsen: Wow. Will Bales: A couple years ago, that was heresy and was a point of much debate. But now it's-
Simon Arthur: Yeah, I remember when Bronco did that the first time.
Will Bales: Exactly. Bronco was the first. In fact, they went one step further. They had an aluminum frame and a titanium frame. So when they were up against big, scary horizontals, they ran the titanium frame, and then when they were up against anyone else, they ran the aluminum frame. They had more weight for armor.
Greg Paulsen: I'm linking the next question with this conversation, by the way, which is trends over time. Yeah.
Will Bales: Yeah. So this is a great trend of that year, people lost their minds about, "Well, it's not fair. It's not the robot. It's not the same robot. It's not competitive, yada, yada, yada." But fact of the matter is, now that there's robots who have double-digit fights over a season, if you have 10, 11, 12 fights, you need more than one robot. So this year, we showed up with two robots and a third in spares. By the end of the event, we had two of them sitting next to each other, and the third frame was sitting flat packed in the corner, just in case we needed it. That's what you have to do. We made 16 of these tires, four sets before the event, and we made another 16 while we were there, because we were getting nervous about our supply. Some of the things that you end up bringing spares for, you never need, and inevitably the one thing you didn't think you need, you needed the most. Yeah.
Greg Paulsen: Yeah. So that's something that … Not for you all, but we may have had some situations during this season where we had to pull some emergency runs, where it's like, "I didn't think that I was going to break that," and figure out some solutions, including, to your point, you were talking about some features that were virtually machined. We had to substitute with Ultem, actually, from a Delrin machined part, because the physical act of machining that replacement component would be longer than what they needed between matches.
Will Bales: Right.
Greg Paulsen: So we substituted 3D printing in, just to keep stuff running. So this is actually a really great time. I'm seeing some great questions coming in. I have one more question for you, Will, before we go to the live Q and A. So for the audience here, keep those questions flowing. We're going to try to capture much as we can. I know I'd said, "Oh, the last half of the hour," and we're already at 6:14 Eastern here. But we'll do our best. So just the story, you started with First Robotics. How does someone get into robotics, and what do you do when you grow up? Where does that path lead career-wise? Will Bales: To start, the simplest thing you can do is do something. Do any kind of thing, if it's Mindstorms kits, the First LEGO League, if it's First Robotics or Vex Robotics. Those educational programs are a great way to start. It's how I started. It's how many of the builders started. It gets you in the right group of people, and it gets you in the right mindset and helps you build the path towards where you want to go. If you want to be a renegade and want to just start building little fighting robots, you can build a one-pounder or a three-pounder. Not all the fighting robots in the world are giant 250-pound scary things. You can start a little bit smaller much faster, much more affordably, and there's competitions all the time. Simon mentioned one at the beginning of the
Simon Arthur: Robot Battles.
Will Bales: Yeah. Robot Battles. It's a hoot. Let me tell you. It's a whole ordeal.
Simon Arthur: Best audience for all robot fighting is at the Robot Battles.
Will Bales: It's a great audience. So you can go to Robot Battles. You can go to all sorts of different little events. But just start making things. I think that's the best thing. Then once you figure out how to make stuff and you want to figure out how to make parts, let's say you need some sheet metal parts made for your robot, well, now you know how to make sheet metal parts for engine mounts if you want to go into cars or housings for medical device components or something like that. Once you start learning how to build all these parts and put your robots together, you quickly realize that everything's a robot project in one way or another. As long as you're making parts, it's all the same skills. So at least for me, that's how I ended up in medical device R and D. It's just making prototypes, and they're just weird-looking robots.
Greg Paulsen: I think … Oh, go ahead, Simon. Yeah.
Simon Arthur: Go ahead. Oh, this past weekend, so I got my six-year-old to draw a picture of the robot she wants to build. Okay? Then the next step, we took that to the next step. We cut the pieces out of paper and taped them together so we have a little cardboard-y design CAD model of the robot. So we'll see if we can take that onto the next step after that.
Greg Paulsen: By the way, I live in advanced manufacturing day in, day out, and there's absolutely nothing wrong with cutting something out of a cardboard and just kind of looking at the room. It will tell you so much. Prototyping in general tells you so much if you just give a little bit of an effort, because we always let perfection get into the way of good enough sometimes. Just highly recommend. Yeah, and by the way, Will, you were mentioning, I think before that, your full-time career, your medical device development career actually came through networking within the robotics fighting community as well. So it's awesome. It's good people, good people. So let's jump into some Q and A, and we have like 15 minutes on the clock here. While I'm looking through some of these questions, I've got just an easy one for you, HyperShock. Where did the name come from?
Will Bales: Oh, HyperShock was the least hated name.
Greg Paulsen: Least hated name. Will Bales: We were trying to figure out what we wanted to name the robot, and we had some plans to call it like Kudi Gras, but some people called it Kudi Gras and some people called it Kudi Gras, and when the name was supposed to be the phonetic spelling and you couldn't agree on how to pronounce it, that didn't work. So we made a batch of spreadsheet of prefaces and suffixes. We said it needs to be three syllables so you can chant it, HyperShock, and the last syllable needs to be the strongest syllable. Then we just kind of voted, and the one we hated the least was HyperShock.
Greg Paulsen: I mean, that works. Yeah, no, it makes a lot of sense. Just on that, HyperShock, you've got a look. It's got a look to it. It's got a brand. There's a question from Tom here on that, which is just the digital branding. Where did that focus come from, and what was the inspiration there?
Will Bales: I mentioned that we want to build a toy, right? We want something that's worthy of being a toy, and because it's a passion project, we want to make something that we're proud of. So especially in season three, when Isaac Lubarsky joined the team, he's the graphic designer. He does all the logos, and he and I work together to figure out what the aesthetics of the robot should be. We knew we wanted to be loud and vibrant and aggressive and robot spaceship, sea creature, alien-looking shapes. So he and I sit down, and we'll export SolidWorks and Blender models back and forth and we'll draw over things and sketch stuff. We spend probably just as much time as other people do designing their whole robot just figuring out the top armor and how everything flows, because it's important to us. But then when you see the final project, it looks pretty good.
Greg Paulsen: Actually, we got some questions on that, and you mentioned you use SolidWorks for your CAD environment, for most of the design integration there. Just a couple folks asked about software, the software side. I will say this. I've noticed where electrical engineers get in the design because they're so frustrated that there's nothing that really fits what they need to design, and especially in robotics, that's kind of where you get into the electromechanical system. So just tell me what type of software platforms you use, and how did you familiarize? What came first mechanical or electrical?
Will Bales: Mechanical came first for me. First, it was paper and then cardboard and then finally SolidWorks for 3D CAD. If I'm doing electronics, which I try to do as little as possible, but this year I had to do some custom circuit boards using KiCAD, KiCAD. It's free open source. If we're starting to do the aesthetic stuff, I've been using Blender, also free open source. A lot of teams use Fusion 360. Some are using Onshape. So you don't have to use one over the other. I like SolidWorks. I've used it since I was like 14 years old, so I'm really good at it and it sense to me. That's what we use at work. It's what we use for robots. But you can do a lot with pretty much all the CAD packages.
Greg Paulsen: Yeah, absolutely, and a fun story. Xometry has free add-ins for SolidWorks, Autodesk, and Fusion 360. Yeah, so what's nice about that is we showed a little bit earlier that demo of the instant pricing that happens on our instant quoting engine. Imagine you're designing a part and you're designing a CNC machine part, and you're like, "I love fillets." You look at the price of it, and then you add all your fillets. Then all of a sudden, you're like, "Hey, my CNC part prices jumped by $250," and it turns out your entire part is now a surface component. There's something really powerful about knowing the actual cost of the item during the design phase, and that's where addeds really come into play.
Greg Paulsen: I'm also going give an obligatory plug as we're jumping in here, which is we do have a discount for those who have stayed on for this. So if you are looking to try Xometry out for the first time or you're just already a Xometry customer and love it, love Xometry, you want to save 25 bucks, I've got a code here, the 2TYRWEBB5. I will not try to pronounce it, but you can read it on the screen there. Simon Arthur: We love robots.
Greg Paulsen: Yeah, please let us cut your robot parts as well. So let's run through a lightning round here. Again, thank you all for the questions coming in. I know it's hard to squeeze a lot of this in an hour, so we're just going to run through. Question from James. It's actually a question from James's 10-year-old son, which is, "What's your favorite fight? What's most memorable?"
Will Bales: I can't tell you yet. Greg Paulsen: Ooh, all right. Stay tuned for this season of BattleBots on Discovery.
Will Bales: Can't tell you yet. I want to. I want to so bad, but I can't tell you yet.
Greg Paulsen: No spoilers, kids. All right. So stay tuned. That's really great. By the way, I had lots of comments on the rake and other things.
Will Bales: Yeah. The rake was great. I have a new favorite.
Greg Paulsen: Yeah. So Sophia asks, "I remember using an RC car controller for HyperShock. Why do you use a RC controller versus a two-thumb stick?"
Will Bales: Before I robots, I'd play with RC cars, and so it made sense to me, especially with an RC car kind of like robot, that the pistol grip transmitter that I'd used in RC cars would help me drive my robot around. I like it a lot, because if I pull the trigger, especially with how much grip we have in the wide wheel base, when I pull the trigger, it goes straight. It doesn't veer off. It doesn't do anything. It goes straight. If I turn the wheel, it turns.
Will Bales: The other thing is when you're up there fighting, I've done this for way too long now, and every time I get the jitters and I don't have the motor control to not freak out and have my thumbs jittering all over the place with those little joysticks. So to me, it's the best solution for driving a robot around. The only caveat is it's a lot harder to do other stuff. So I have a teammate, Kyle, who's running the weapon, and he and I talk together to make sure that the weapon's at the right speed given a time. But yeah, pistol grip for life. That's the way to do it.
Greg Paulsen: So when you're driving, and just on that note, there's a couple other people that are controlling other aspects of HyperShock. Yeah. It's their dealer's choice, too, on what they're using for control. I do have a question just from future roboticists here, which is just sourcing motors and stuff. Are there any tips? I'm going to generalize like five questions about people just saying, "Where do you get your stuff?" But what are your favorite spots?
Will Bales: Every year except for this year, we've done new motors and new controllers because we were unhappy with something about the last one. This year, that changed, because we finally have a motor and controller package that we really like. So for the techie folk, here's what it is. For motors for the drive train and the weapon, we're using Neumotor, N-E-U, Neumotor 8038s, 100 KV versions. For the motor controllers, we're using the VESC 75300 made by Trampaboards. It's a great package. We're running censored with the AS5147 P-chip, as you know, and there's two for the weapon and one for each side of the drive. So we have four of the same motors, same controller, and the robot makes it really easy to swap things out. A lot of other robots still are using the tried and true Magmotors or AmpFlows that are brushed. They're a little less efficient. They're a little bit heavier. But if you're scared of programming and fine tuning things, it's a good bulletproof way to go. Greg Paulsen: Just on that note, are these motor components, are they secure to the frame, or how are they secured against impact and that sort of stuff?
Will Bales: So there's a thing called battle hardening that people do, where they take the motors apart. They goop on epoxy and cross their fingers that the magnets aren't going to blow up and that the windings aren't going to catch fire. I'm lazy, so I decided to shock mount everything. So this is a motor pod. This is either the left or the right side of the robot. It's mirrored, just swaps to one side. It's chain drive, and we have a motor. We have the encoder here. We have the motor controller, and it's just a block. Then these round cylindrical black things are shock mounts.
Greg Paulsen: Dampeners. Yeah. Will Bales: Gloves, colloquially in robot world.
Greg Paulsen: Are those custom dampeners, or is that like actually an off the shelf component?
Will Bales: This is a McMaster part. It's great.
Greg Paulsen: McMaster. Yeah. Okay.
Will Bales: Yeah. So this is a McMaster part, and we just put big 3816 bolts straight through them into the chassis. That's it. Power four bolts, and that's it.
Greg Paulsen: All right. Will Bales: Works great. Greg Paulsen: So we'll do a couple more questions, and again, thank you all for all these question. Actually, one tensecond thing here. Can you wish Laura a happy birthday, please?
Will Bales: Happy birthday, Laura.
Greg Paulsen: All right. That's great. So apparently Laura's watching this and drifted off after a hard day's work, but her partner asked for a happy birthday there.
Will Bales: Wake up, Laura. Happy birthday.
Greg Paulsen: Wake up, Laura. Watch it on demand. This is going to be recorded, too. So we've seen actually the first episode of season, just everything catching on fire. There's the question that, "Where does fire come from on these machines usually, and what are you doing to prevent that?"
Will Bales: One of these things, batteries, motors, or the controllers, and the biggest reason why things are starting to blow up so often is because of how ambitious everybody's getting to try to be a little bit more dangerous than everybody else. Lithium batteries are incredible. They are energy-dense. They can run your phone forever or they can run a battle bot for about three minutes. But when you're pulling that much current, hundreds and hundreds of amps, they get hot. If you're not doing things right, then they can let all the magic smoke out. Same for the motor controllers. Everything's running right at the limit. There are no safety margins when it comes to BattleBots, because you want every little bit of power that you possibly can.
Greg Paulsen: That makes sense. Yeah, it is so interesting whenever you could tell the weapon hit the battery. It's like black smoke, flames.
Will Bales: Oh, yeah.
Greg Paulsen: Oh, boy. So if you're rooting for … I've got a question here, like, "All right. We get you love HyperShock." It's another one that you root for all the time, and I guess you have a sister robot, right? So would it be that one or still family feud?
Will Bales: So Witch Doctor is on the other side over here. We share a workshop. So if I have to vote for anybody else, it's usually Witch Doctor. There's so many amazing robots, but my personal favorite going into the season was Saw Blaze. I just thought that Jameson had it totally nailed, and it's so scary. To me, Saw Blaze was the one, my choice to win the year.
Greg Paulsen: I think Saw Blaze may be on tonight, maybe. Will Bales: Yeah. Yeah, yeah. The main event tonight.
Greg Paulsen: Saw Blaze is the main event tonight. Yeah. Will Bales: Yeah, Madcatter versus Saw Blaze. It's a good one.
Greg Paulsen: Yeah. So after this, an hour and a half from now, yeah, get your dinner. Watch the event tonight here. On that note, I think, Will, this has just been an amazing hour. I wish we could sit here. We could probably see it for another two hours answering these questions coming in, but really had
Will Bales: I've got time. Greg Paulsen: … a super thorough review. I mean, I could ask if there's another answer that you wish someone asked, go for it, man. But if not, I just really wanted to thank you for the time, and Xometry as a sponsor of HyperShock, just as fans of watching BattleBots and watching real engineered equipment. I mean, this is not unintended, right? That everything about these designs is intentional and well designed and learned through, and you've seen it all. You've seen the material science. You've seen the electromechanical systems. You've seen the design side, and you've seen the sourcing world. So, I mean, it really does culminate all these disciplines when it comes to making real, tangible goods. Any last words, Simon, before we jump off?
Simon Arthur: I think that's it. Yeah, it's been great talking to you guys, and the season has been fantastic so far. Love the look of HyperShock, and hopefully you guys are going to go all the way.
Will Bales: Fingers crossed. We had a great time. No matter what happens, we, it was the most fun we've had this
Keyword: cnc turning
日本三年签证怎么办理?
你喜欢性感火辣豹纹的奢侈品吗?
You May Also Like
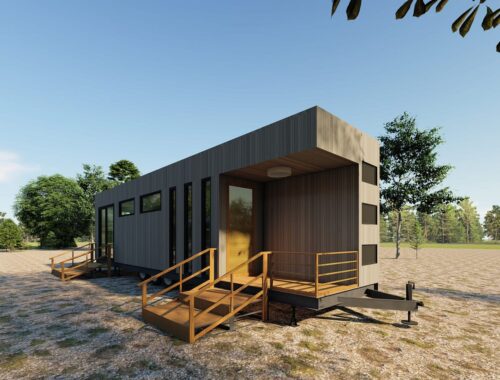
シャーシ設計の最適化手法とその応用
March 20, 2025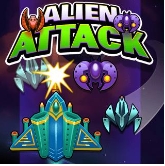
Sprunki: A Comprehensive Exploration of Its Origins and Impact
March 19, 2025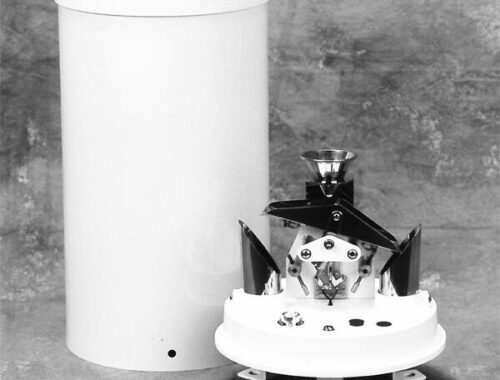