The Production Gap Between Punching and Machining
There are two great manufacturing technologies available: CNC punching and CNC machining. Both have unique advantages and disadvantages, but there is a gap between them that makes it difficult to decide which process to use. This article helps clarify when using CNC punching and CNC machining is appropriate. It proposes a new way to address the gap between punching and machining of short production runs in flat material production.
The Benefits and Advantages of CNC Punching vs CNC Machining
Many CNC punching systems on the market range in size, speed, and capabilities. Generally, CNC punching is ideal for punching two-dimensional holes in flat sheet material for high-volume production runs. The main advantage of this process is the short cycle time per part. One of the disadvantages is the lengthy setup time required to configure the equipment with the many punches required to do a job effectively.
In some cases, a custom punch or die might also be needed. So, the problem lies in facing short to medium production runs. Setting up the equipment can take longer than running your parts. If you factor in the overall time for the job, it isn’t easy to be competitive. What about just machining the part?
CNC machining offers some advantages over punching, but it also has some distinct disadvantages. Typically, the setup times are quicker with CNC machining. However, the actual cycle time to machine the part over punching can be significantly longer. Therefore, it is only viable for a prototype or one-to-two-piece run.
Sometimes, these parts can be large or nested in larger sheet materials, which makes it difficult to secure to the bed of a CNC machine. This requires larger equipment that can be expensive and take up a lot of floor space. A well-equipped machine shop may have a range of different-sized CNC machines that allow flexibility, but what if you don’t? There is a solution that opens the possibility of using CNC machining for small to medium-sized production runs in flat, large-sized sheet material.
DATRON Has the Right Solution
DATRON machining systems offer unique features to bridge the production gap between punching and machining providing advantages over traditional offerings. They allow for the machining of short to medium production runs in flat material and are a viable alternative to punching.
Vacuum Table Systems
The DATRON gantry style design offers a large work envelope for sheet material with a relatively small footprint. Integrated into the machine is a large, unique vacuum table system that has revolutionized the production of these flat parts. A permeable card stock laid over the top of an ‘air hockey’ like vacuum table secures your flat material to the machining table. You can machine precision parts through the sheet material and into the sacrificial card stock.
The vacuum will hold the part without any movement. You can even secure a part about half the size of a dollar bill. There are no gaskets or custom fixturing; just lay down your sheet and hit cycle start. When complete, the machine control turns off the vacuum pump, and the operator or robot removes the permeable sheet off the table with all your precision machined parts on top. Now, the machine is ready for a new card stock and sheet material.
Learn More about DATRON’s Vacuum Tables for CNC Machining Centers and Milling Machines
High-Speed Spindles
The DATRON systems also have a high-speed spindle that allows you to machine at much higher feed rates, reducing the overall part-cycle time. Still, it is a different speed of punching. However, when you factor in the setup time of just a few minutes with the approximately 5x improved cycle time, the overall production time opens the possibility of producing small production runs in sheet material economically.
The 40,000 – 60,000 rpm spindles are capable of tool changes that open more flexibility to punching and reduce the need for secondary operations. Features such as thread milling, chamfering edges, and machining pockets can be done simultaneously. You can even engrave or serialize your parts.
Simple Coolant Systems
There is an integrated spray alcohol mist coolant system that simply evaporates, so you do not have to deal with coolant maintenance or part clean-up. The low-viscosity coolant penetrates right at the cutting tip, accommodating the full potential of a high feed rate from the high-frequency, direct-drive spindle. The coolant system can also accommodate oil lubricants when working with ferrous materials.
Integrated Measuring Probe
Suppose you are dealing with precise Z depth tolerances such as a chamfered edge or an engraving of an identification number just a few thousand of an inch deep. In that case, DATRON has an option for these production challenges. There is a measuring probe that the operator can instruct to quickly take measurements over the entire surface of the sheet and compensate for any surface variants. You program your part as if it were mounted perfectly flat, and the machine Z-axis will automatically raise and lower to follow the surface contour of the sheet. This can also be helpful when dealing with materials that vary in thickness, such as acrylics.
CNC Machining Produces Better Results
Deciding to produce your flat sheet material parts by CNC machining also opens other advantages over CNC punching. You are limited to two-dimensional holes unless you have a very sophisticated punching system. With machining, you now have the capability to machine recesses, countersunk holes, threaded holes, and 3D-contoured surfaces. Additionally, a punched hold tends to have a slightly folded edge to the opening with chaffing on the edges. Depending on the setup, a nibbled punched hole can also leave jagged edges.
Meanwhile, the machined edge is straighter and more pristine. The folded edge is sometimes acceptable because a component bezel or part covers the opening. Our customers have found, however, that the precise, machined appearance of their parts helps them win more business.
Both punching and machining technologies are excellent processes and have expertise in the manufacturing world. When a manufacturer is faced with producing a high volume of flat parts from sheet material, punching is a well-suited technology for this requirement. For a one-piece prototype requirement, traditional CNC machining is the viable approach. Manufacturers are increasingly quoting short-run, high-mix scenarios in flat sheet material parts and face that gap between the technologies. With the DATRON system, there is now an economical and competitive solution for the gap of short-run production requirements in sheet material.
Take Your Project to the Next Level Today!
Now you know more about the production gap between punching and machining. But who can help you get started?
Here at DATRON, we specialize in providing you with the necessary tools. We’re a leading name in the industry, ready to help you take your existing skills to the next level. And if you’re ready, we have everything you need to start. All you have to do is contact us today!
Keyword: CNC machining
You May Also Like
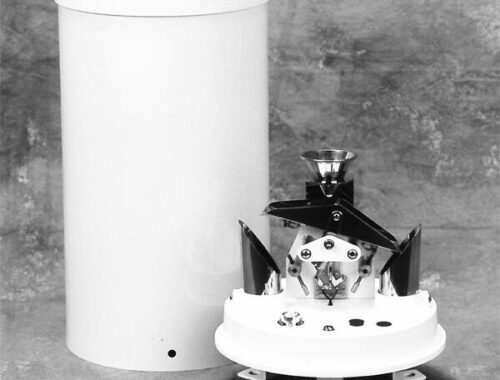
10 Practical Applications of Rain Gauges in Everyday Life
March 20, 2025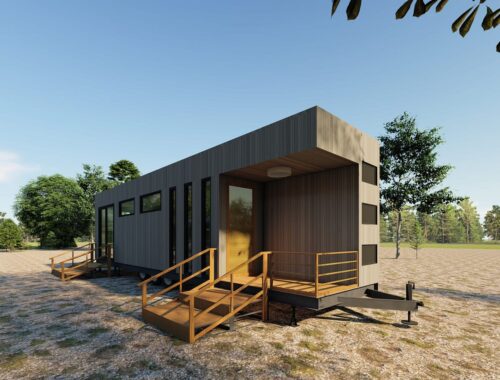
コンテナハウスの魅力と活用方法
March 14, 2025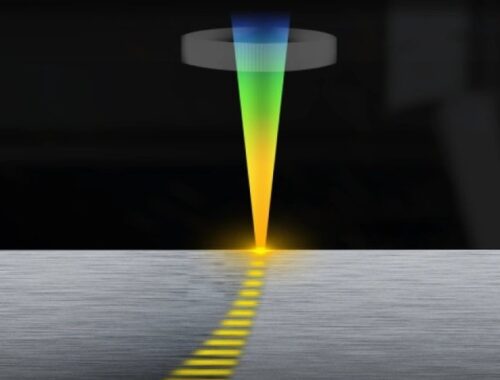