Swiss Machining: Precision and Efficiency in Small Part Manufacturing
# Swiss Machining: Precision and Efficiency in Small Part Manufacturing
## What is Swiss Machining?
Swiss machining, also known as Swiss screw machining or Swiss turning, is a specialized type of precision machining that originated in Switzerland’s watchmaking industry. This advanced manufacturing process is designed to produce small, complex, and high-precision parts with exceptional accuracy and repeatability.
Unlike conventional lathes, Swiss machines feature a sliding headstock and guide bushing that provides superior support for the workpiece, allowing for tighter tolerances and better surface finishes on long, slender parts.
## Key Advantages of Swiss Machining
### 1. Exceptional Precision
Swiss machining can achieve tolerances as tight as ±0.0002 inches (0.005 mm), making it ideal for components requiring extreme accuracy. The guide bushing system minimizes deflection, ensuring consistent quality throughout production runs.
### 2. High Efficiency
These machines can perform multiple operations simultaneously, including turning, milling, drilling, and threading. This multi-tasking capability significantly reduces cycle times and increases productivity.
### 3. Cost-Effectiveness for Small Parts
For high-volume production of small, complex components, Swiss machining often proves more economical than traditional CNC turning due to reduced material waste and faster production times.
## Common Applications of Swiss Machining
Swiss machining is widely used across various industries that demand precision small parts:
– Medical devices (surgical instruments, implants)
– Aerospace components
– Electronics and connectors
– Automotive parts
– Watchmaking and jewelry
Keyword: Swiss Machining
– Defense and firearms
## The Swiss Machining Process
The unique design of Swiss machines allows for a distinctive workflow:
1. The bar stock passes through a guide bushing close to the cutting tools
2. As material is removed, the stock is fed forward through the bushing
3. Multiple tools can work on the part simultaneously
4. Finished parts are cut off and collected
This process enables machining of parts with diameters as small as 0.5 mm while maintaining excellent dimensional stability.
## Choosing the Right Swiss Machining Partner
When selecting a Swiss machining provider, consider these factors:
– Experience with your specific industry requirements
– Quality certifications (ISO, AS9100, etc.)
– Material capabilities (metals, plastics, exotic alloys)
– Secondary services (heat treating, plating, assembly)
– Prototyping and production volume flexibility
Swiss machining continues to evolve with advancements in CNC technology, tooling, and automation, making it an increasingly valuable solution for precision manufacturing challenges.
传奇3手游:重温经典,再战沙城
You May Also Like

Google Snake Game: A Classic Arcade Experience
March 23, 2025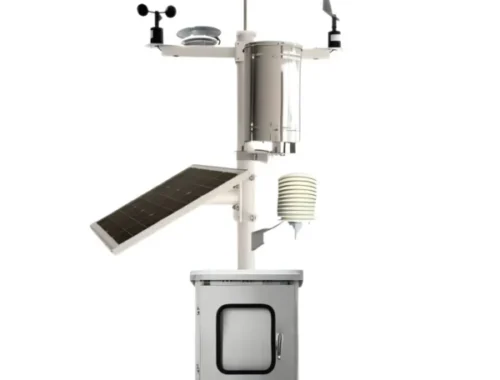
Automatic Weather Station: An Overview of Its Functionality and Applications
March 14, 2025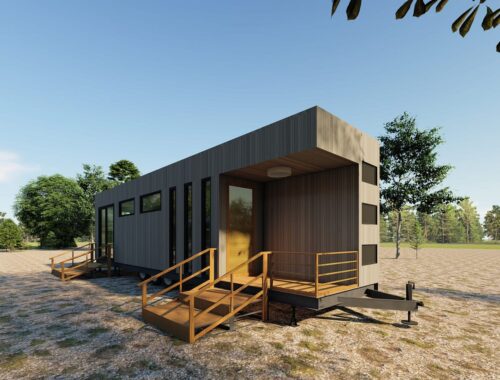