How OluKai Makes Its Hand-Dyed Indigo Kicks
>
Want true one-of-a-kind footwear? OluKai’s new Hawaiian Blue indigo shoes are literally that. The canvas slip-ons from the Aloha State–born brand are made from fabric that is hand-dyed by a pair of Hawaiian artists. No two are the same.
OluKai is known for its Hawaiian coastal-inspired footwear. The company makes sandals and sneakers that are designed to function in and around water and often sport patterns drawn from the landscape, many created by island artists. The indigo special edition is the result of a partnership with Hawaiian Blue, a pair of artists who use indigo to hand-dye everything from dresses to dish towels.
It’s a complicated process that takes several days. It starts with the leaves of the Indigofera suffruticosa plant, which Donna Miyashiro and Tokunari Fujibayashi grow in their front yard. They harvest the leaves just as the plant blooms, then soak them in water for roughly a day to ferment. The fermented leaves produce a yellowish-green paste that settles in the water over multiple days. As it settles, the artists skim water off the top until all that’s left is the paste, which forms the base of the dye. The process takes about three months from seed to first dye.
Rather than dye the fabric in a single shade of blue, Miyashiro and Fujibayashi use a special stitching method called shibori, pulling and gathering the fabric to create a tie-dye-like pattern. Each piece of fabric gets submerged in a vat of dye between three and five times and is then aired out to oxidize, which makes the dye turn blue.
“It’s a closed-loop, sustainable system,” says Kerry Konrady, vice president of marketing at OluKai. “They plant, grow, and harvest their own indigo and then hand-dye each yard of fabric individually.” Because of the homegrown nature of Hawaiian Blue’s operation, OluKai had to work with them to scale up their production enough to yield a full batch of shoes.Still, it was slow going. Hawaii Blue’s dye vats are only big enough to fit one square yard of fabric. It took a week and a half to dye five pieces.
Once dyed, the fabric was shipped to OluKai’s factory, where it was sewn into shoes. “Indigo dyeing holds a special place in our hearts because of the beauty and depth that emerge from the vat each time a piece of fabric is dipped,” Miyashiro says. “To see the fabric come out a yellowish green and transform into ‘Hawaiian Blue’ as it is fanned into the air is mesmerizing.”
At the very least, the shoes’ dreamy blue pattern has us all dreaming of our next beach vacation.
Buy Now
You May Also Like
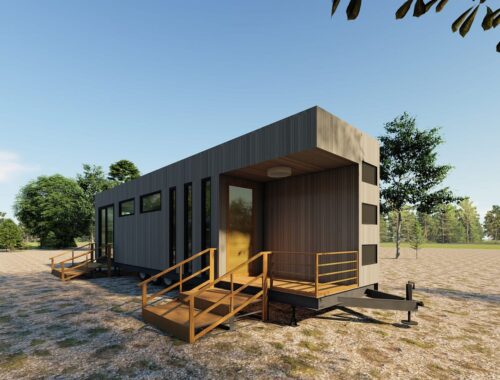
ユニットハウスのメリットとデメリットを徹底解説
March 20, 2025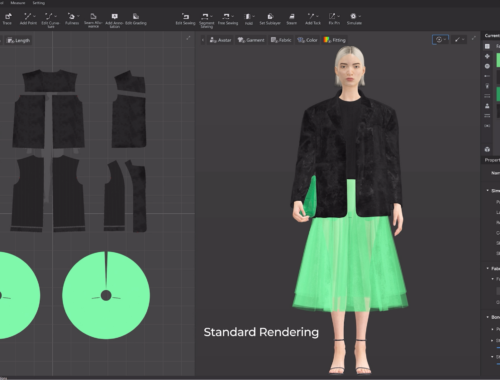
The Future of Fashion: How Artificial Intelligence is Revolutionizing the Industry
February 28, 2025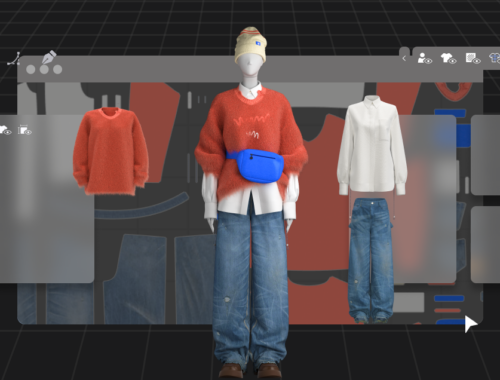