Effective Ways to Prevent Screw Slippage
Many customers have encountered many questions when using twin-screw extruders, such as why the products produced by twin-screw extruders are defective, and what to do with their screw slipping. If there are any problems, the following editor will take you to briefly understand the knowledge about this aspect.
1. The back pressure of the extruder screw is too high
If the back pressure is set too high, then the extruder screw may not be able to generate enough pressure to transport the melt forward to overcome the back pressure of the back pressure, and the extruder screw will rotate in a certain direction without retreating, which will cause Doing more work on the melt and significantly increasing the melt temperature then adversely affects finished product quality and cycle time.
2. The second half of the extruder barrel is overheated or undercooled
At the rear of the feeding section, the material forms a thin layer of molten polymer during the heating and compacting process. The molten film layer is attached to the extruder barrel. Without this thin layer, the pellets would be difficult to transport forward. The material in the feeding section must be heated to a critical temperature to produce an important molten film layer. Often, however, the residence time of the material in the extruder barrel is too short to allow the polymer to reach this temperature. This may happen because the equipment design is too small, and the corresponding equipment is composed of a smaller extruder barrel and screw. A residence time that is too short can easily result in insufficient melting or mixing of the polymer, which can then cause the extruder screw to slip or stall.
3. Extruder barrel or screw wear
As in the feed section, the resin adheres to the barrel wall as it melts in the extruder screw constriction section. When the extruder screw rotates, the material is subjected to shearing force and then breaks away from the extruder barrel wall and is transported forward. Assuming there are wear zones on the extruder screw and barrel, the extruder screw elements cannot transport material forward.
4. Improper design of extruder barrel and hopper
Correct hopper design is the key to ensuring stable material transport. In general, fresh pellets of uniform size work well in square hoppers with abrupt compaction zones. However, this is not the case when admixing recycled materials. By re – disrupting the pellets are very inconsistent in shape and size, which affects the uniformity of the feed. Inconsistent feed means that the extruder screw cannot maintain a uniform transport pressure on the melt and slip occurs.
5. Extruder screw processing hygroscopic materials
Improper drying of the material can significantly reduce the viscosity of the material in the extruder barrel and generate water vapor, making it difficult for the extruder screw to transport the material forward.
6. Failure of the screw check ring of the extruder:
When the extruder screw is rotating and plasticizing the material, the non-return ring should be in the front position, touching the fixed ring seat. If the non-return ring is in the backward state, or a state in between forward and backward, the molten polymer will have resistance when passing through the gap between the non-return ring and the ring seat. If a problem with the non-return ring is suspected, it should be replaced immediately.
LESUN is specialized in the production of parallel co-rotating modular screw elements, barrels and screws, covering various models from Ø20mm to Ø300mm. After ten years of vigorous development, our company now has a number of advanced CNC machine tools and special processing equipment for screw manufacturing. Now our machining operations are basically intelligent and automated. Advanced processing methods, strong technical force and sophisticated processing technology ensure that the quality and technical indicators of each production fully satisfy customers. If necessary, welcome to consult.
Keyword: screws & fasteners world
You May Also Like
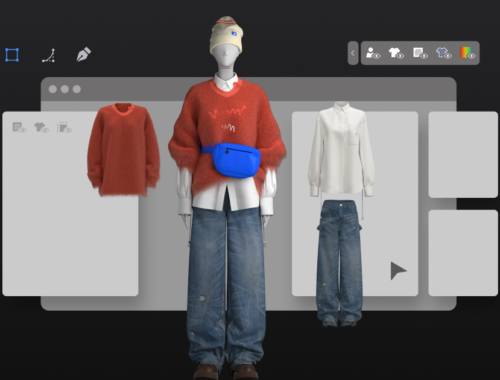
AI in Fashion: Transforming Design, Shopping, and Sustainability for the Future
March 1, 2025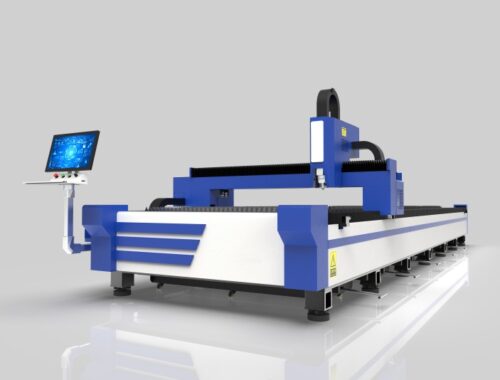
DO YOU KNOW HOW TO EXTEND THE LIFESPAN OF YOUR LASER CUTTING MACHINE?
November 22, 2024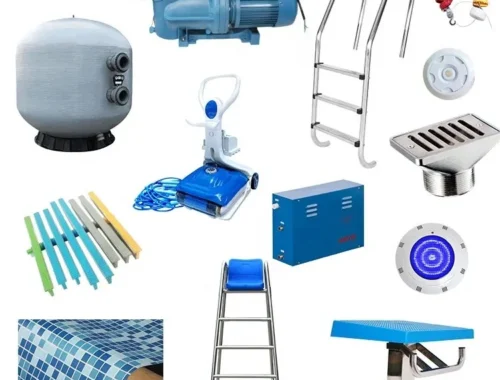